Traditional craftsmanship meets modern technology
Our process lets us build a very wide range of items, using an extensive catalog of materials and techniques. Our work is an act of collaboration between skilled humans and our advanced machinery.
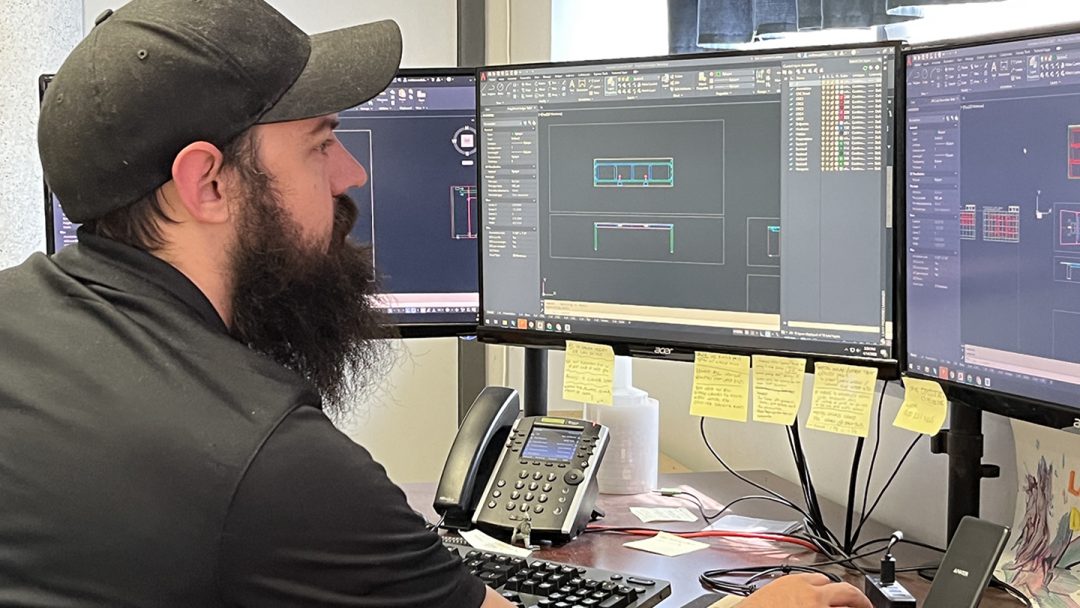
Design & Engineering
We get some of our designs from clients, some we develop ourselves. We tailor our process to the needs of our clients. We document our concepts using 3D images, and shop drawings. Our project management team oversees samples and communications with the clients. The engineering team works with the shop floor workers to identify the best methods for each job. Then they make detailed drawings of every part of the project, for our people to use, and a set of files that drive our CNC router. Before any begin production, there are extensive reviews with the design engineer, the project managers, the engineers, and the shop foreman.
Choosing Materials
We work with our clients to identify which materials they prefer. Our Project Managers send out samples so that clients can see how those choices work in their space. The final material choice happens on the shop floor. When our cabinetmakers take their plans to the woodpile, they are evaluating the pieces they need to make against the actual characteristics of each board. Color, figure, knots, and other character marks will determine how we use each piece. A highly skilled person needs to look at every piece and plan how to transform it into the required part.
There is also considerable variation in the other materials we use. Metals, stone, glass, laminate – even if they come out of the same factory, the individual pieces are never identical. And our manufacturing process will introduce stresses that have to be taken into account when planning material yields. Our skilled and experienced cabinetmakers work hard to get the best results from every material.
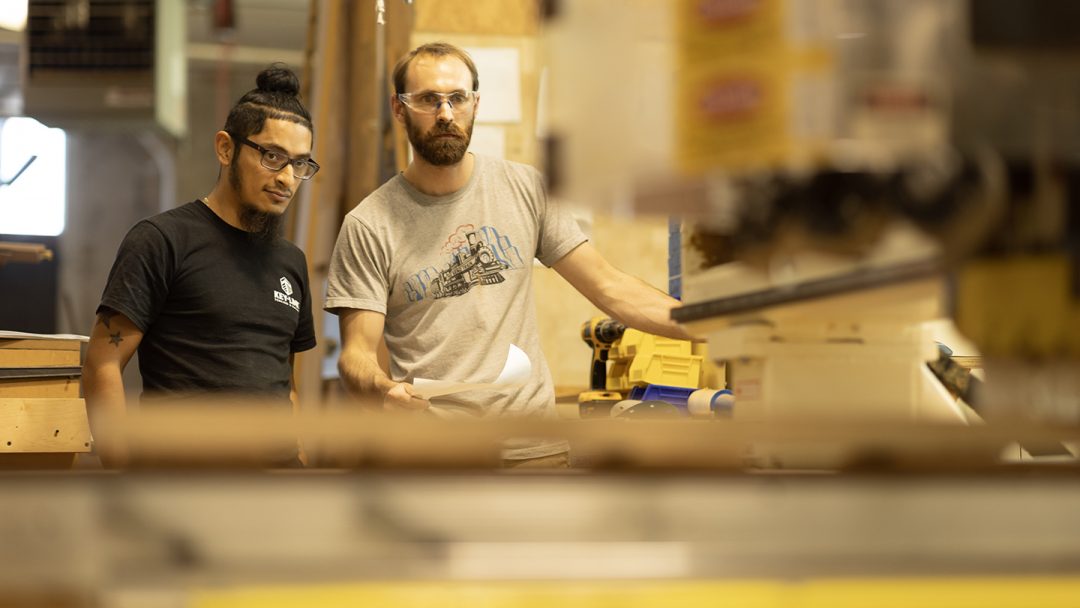
Making Parts
In a modern workshop, machines do the cutting and skilled people do the assembly. We use our CNC router to cut parts in every project. It is extremely accurate. We can be sure that all of the parts for a complex piece will fit together perfectly.
We have a variety of other machines to cut, drill, glue, and shape wood and metal. We are equipped to execute hundreds of different manufacturing processes. Many of our machines are designed to do a single process in high volume. Our skilled operators allow us to efficiently do the short runs required for custom work. After machining, every part is carefully examined for quality and then placed into sets on a cart with the other parts of the same job. These carts are queued until a cabinetmaker starts work on that project.
Initial Assembly
Machines are great at accurate cutting, but they cannot put things together. Only highly skilled human hands can perform all of the tasks required to fit, glue up, sand, and check our work. We make complicated objects, with multiple sub-assemblies that need to be built and then fit together. Our build process culminates with a complete assembly of each piece. We check that everything is beautiful, smooth, and fits together perfectly. We check the hardware, and any A/V equipment in the project. Our project managers then do an independent quality check so that everything is just so. Then it’s off to the finishing room.
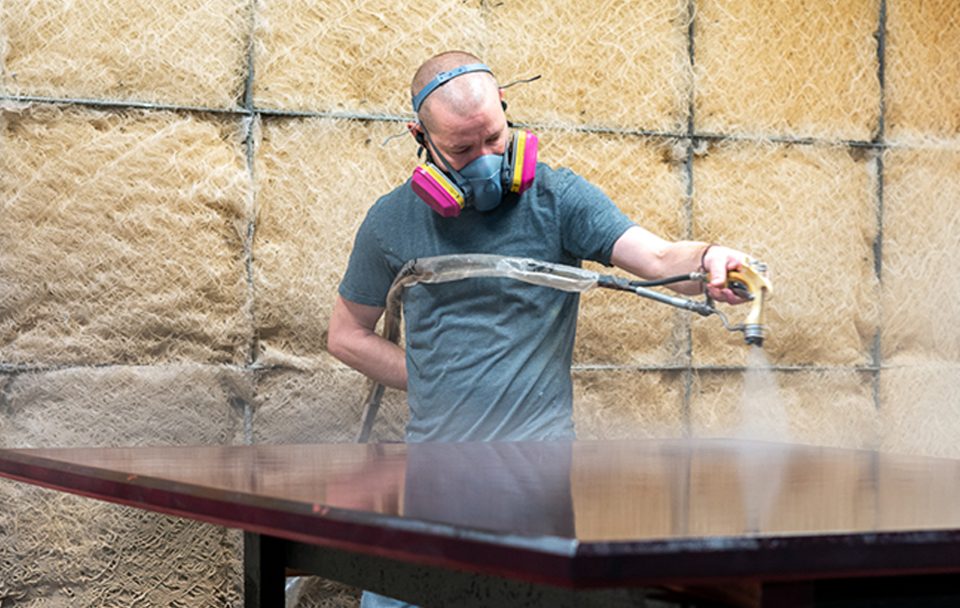
Finish & Sealant
Wood needs to be finished to protect it from wear and dirt, and to bring out the beauty of the grain. There are countless ways to finish a piece. We can choose from a huge variety of different types of finish, and each of these can be applied in multiple ways. We can also color the wood using stains, paints, or dyes. We can finish parts of a piece with one finish and other parts with another, to achieve a mix of textures and colors. All of these processes are performed by our highly skilled finishers.
Final Assembly & Inspection
After the finishing is done, we re-assemble each piece to check that everything works. Once again, the project managers go over every detail to ensure that all is as it should be. We check the fit of all the parts, and the hardware, and the overall appearance. We also take a lot of photos of the completed conference room table for our records. Then the table is disassembled for packing.

Packing & Shipping
Most of our clients are located far from our shop. We ship tables all over the continent and the world. Nobody wins if there is damage in transit, so we take extraordinary care to pack and ship our work.
After the finish inspection, the piece is completely disassembled again. Each component is cleaned with a disinfectant mixture. Then we wrap each piece in foam and encase that with a cardboard outer layer. All edges are reinforced with corner protectors. The wrapped pieces are then placed on a custom made pallet, and strapped together with steel strapping and shrink wrap. Every item on the pallet is labeled, and the overall contents of the pallet are recorded in our database. We photograph the pallet at multiple points in the process. Finally, we add an outer wall to the pallet, leaving the top open.
Our pallets travel the country via LTL trucks. We usually ship to an installer who will receive the pallet and complete the installation. Many of our clients choose to do their own installation. The design engineers and project managers discuss the installation process very early in the project, to make sure that everything goes well from start to finish.
Subscribe
Stay in touch with us and hear about our latest projects.