How We Get it There
Everything we make is unique. We have one chance at a successful delivery. Making sure everything arrives on time and in perfect condition is critical.
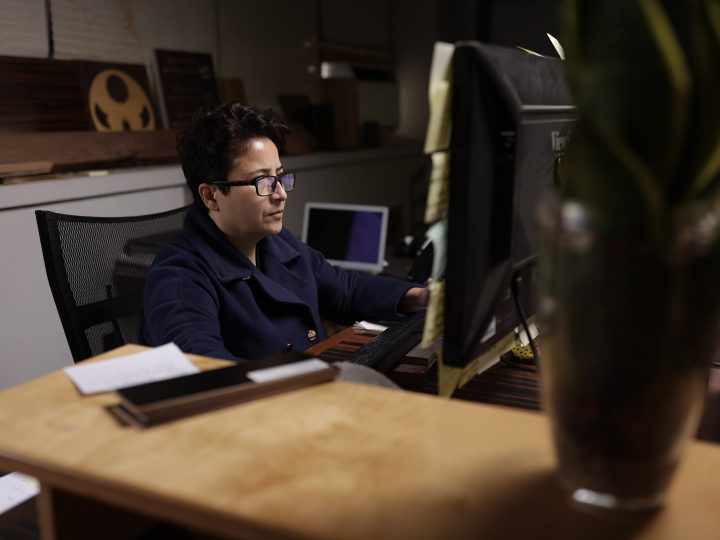
Planning
All of our work is designed to be easy to deliver and assemble. This starts at the beginning of the design process. Our Design Engineers consider how a large object can be made in multiple pieces, and double check to make sure that every piece can fit through a standard door. Project Managers are tasked with confirming the delivery path from the loading dock to the final position, and identify every issue that might prevent a successful installation. If we are outsourcing installation, PMs also prepare a custom set of assembly instructions that show the installer exactly how to put the work together.
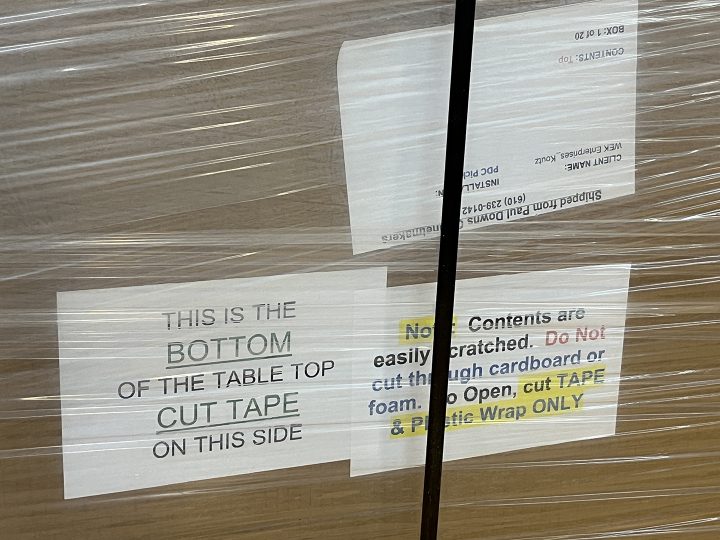
Packing
Each job is made in multiple pieces. After the pieces is assembled for final inspection, every component is cleaned and individually wrapped. We use a base layer of foam, and then wrap each piece in cardboard, with heavy edge and corner protectors where needed. Every piece is labelled. We do more than note part numbers – critical components, like top pieces, have very clear indications as to how they should be handled, and what to avoid.
Crating
If we aren’t doing the delivery ourselves, all of our jobs get a custom crate. This is sized to hold all of the parts, but no larger, to save on shipping costs. Crates consist of a pallet base, and after all the parts are strapped to that, we wrap the crate with OSB walls. The crate is weighed, and then we book a truck. Clients are given complete tracking information.
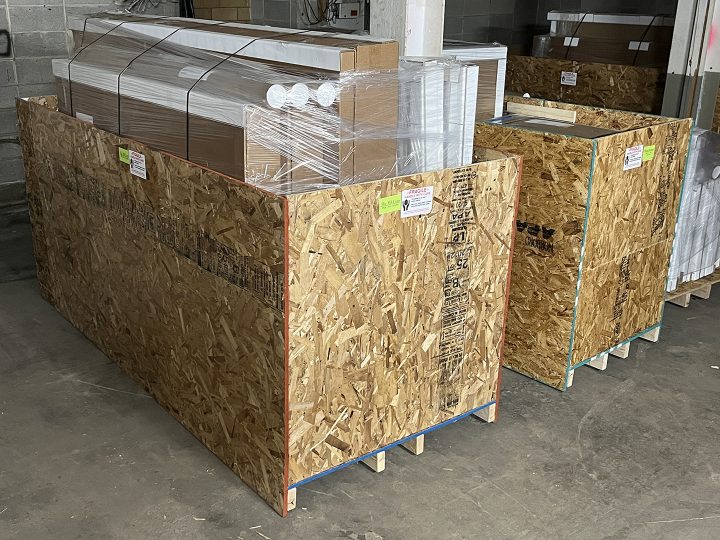
Shipping
We use commercial trucking services to move our work from the shop to wherever it has to go. Our crates are designed to withstand the rough treatment that over-the-road shipments experience. The side walls protect against damage from forklifts and other cargo. And we never, never put a top on our crates, so that truckers can’t stack another shipment on ours. We’ve been shipping our work for decades, with an extremely high success rate. Less than .1% of our shipments have ever experienced any damage in transit.
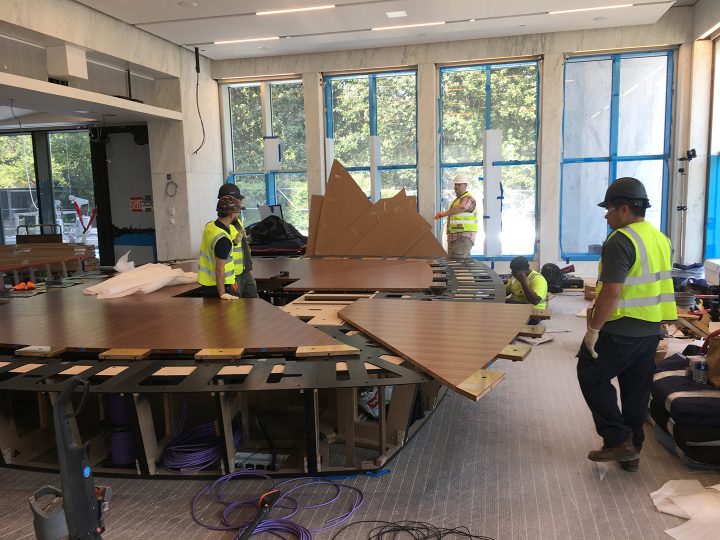
Delivery
We often deliver jobs using our own trucks, particular when the client is less than 200 miles from our shop. We still wrap every piece of each job with foam and cardboard, but the crate is a little different – no side walls required. Our skilled cabinetmakers then bring the piece into the final destination and put it together.
If delivery is being performed by contracted installers or furniture dealers, and the job is complex, we can send our own supervisors to oversee the installers. But the vast majority of our jobs go together without a hitch, and without the additional cost of supervision.
Installation
We work very hard to ensure that anyone assembling one of our tables is having the best, easiest experience they’ve ever had. We’ve heard it over and over again: professional installers are blown away by the care and quality of our packaging, and how quick and easy it is to put the work together.
No need to take our word for it – watch the video for feedback from a veteran union installer.
Stay in touch with us and hear about our latest projects.